As the coronavirus pandemic began to surge this spring, hospitals scrambled to provide essential workers with enough personal protective equipment (PPE) to wear while treating patients.
When Northwestern researchers Chad A. Mirkin, the George B. Rathmann Professor of Chemistry, and David Walker ’14 PhD, a former postdoctoral associate in Mirkin’s lab and an entrepreneur-in-residence, heard about the PPE shortage, their team sprang into action. Just months prior, in fall 2019, Mirkin and his research group had unveiled a new 3D-printing technique they invented called “high-area rapid printing,” or HARP. Using the technique, a 13-foot-tall printer with a 2.5-square-foot print bed can print about half a yard of material in an hour — a record throughput for the 3D-printing field. Come spring, HARP proved to be a solution for producing face shields at high volumes.
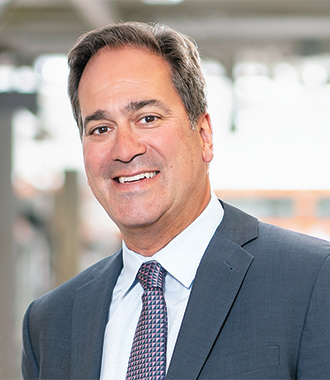
Northwestern researcher Chad Mirkin and his team are using a new 3D-printing technique to produce face shield components.
“Even fleets of 3D printers are having difficulty meeting demand for face shields and other PPE because the need is so enormous,” says Mirkin, who also is director of the International Institute of Nanotechnology at Northwestern. “But HARP is so fast and powerful that we can put a meaningful dent in that need.”
Face shields comprise three components: a sturdy plastic headband, a clear plastic sheet and elastic. The plastic sheet clips into the headband, which is then secured to a wearer’s head with a stretchy elastic band. HARP produces PPE parts at a rate of 1,000 per day by running the printer round-the-clock. Volunteer team members work in six-hour shifts to keep the production cycle going continuously.
Along with fellow Northwestern researcher James Hedrick ’19 PhD, Mirkin and Walker founded Azul 3D Inc. on the technology underlying HARP, which they licensed from the University with the help of the Innovation and New Ventures Office (INVO). The Azul 3D team leads the headband printing and has partnered with a local manufacturing company to provide the laser-cut, clear plastic shields. A third partner sanitizes and packages the face shield components into easy-to-assemble kits, which are supplied to Chicago-area hospitals. The face shields can be washed and reused.
HARP relies on a new, patent-pending version of stereolithography, a type of 3D printing that converts liquid plastic into solid objects. It prints vertically and uses projected ultraviolet light to cure the liquid resins into hardened plastic. These continually printed parts are mechanically robust and can be used for cars, density, sports equipment and more. HARP will be available commercially in the next year.
As of the end of June 3,886 face shields had been shipped to seven states in need, including Illinois. Most were sent to the Navajo Nation, which has one of the highest rates of COVID-19. Materials also have gone to hospital COVID-19 wings and emergency rooms, first responders, private medical offices, COVID-19 research laboratories, nursing homes, outpatient nurses, skilled nursing facilities, pharmacists and funeral homes.
A gift from actor Johnny Galecki of The Big Bang Theory helped make Mirkin and Walker’s project possible.
Reader Responses
No one has commented on this page yet.
Submit a Response