A tiny break-dancing robot could be the future of medicine, manufacturing and environmental cleanup. Developed in the labs of Samuel I. Stupp ’77 PhD and Monica Olvera de la Cruz, the centimeter-sized robot can walk at human speed, pick up and transport cargo to a new location, climb up and down hills and then perform a spinning break dance to release the cargo. Resembling a four-legged octopus, the robot functions inside a water-filled tank, making it ideal for use in aquatic environments. Researchers imagine customizing the robot’s movements and locomotion to precisely deliver biotherapeutics or catalyze chemical reactions to yield products. It also could be designed to recognize and remove unwanted microplastics from the environment or blood clots from delicate tissues.
“Conventional robots are typically heavy machines with lots of hardware and electronics that are unable to interact safely with soft structures, including humans,” says Stupp, the Board of Trustees Professor of Materials Science and Engineering, Chemistry and Biomedical Engineering. “We have designed soft materials with molecular intelligence to enable them to behave like robots of any size and perform useful functions in tiny spaces, underwater or underground.”
Nearly 90% water by weight, the aquatic robot is made from a first-of-its-kind, soft, lifelike material, invented in Stupp’s lab. Its sea creature–like movements come not from complex hardware, hydraulics or electricity. It is activated by light and walks in the direction of an external rotating magnetic field. Within its water-filled structure is an embedded skeleton made of aligned, ferromagnetic nickel filaments. The resulting robot is a molecularly designed network, with parts that allow it to respond to light, hold or expel water and have just the right stiffness to respond rapidly to magnetic fields.
“By combining walking and steering motions together, we can program specific sequences of magnetic fields, which remotely operate the robot and direct it to follow paths on flat or inclined surfaces,” says Olvera de la Cruz, the Lawyer Taylor Professor of Materials Science and Engineering, Chemistry and Chemical and Biological Engineering. “This feature allows us to direct the robot through narrow passages with complex routes.”
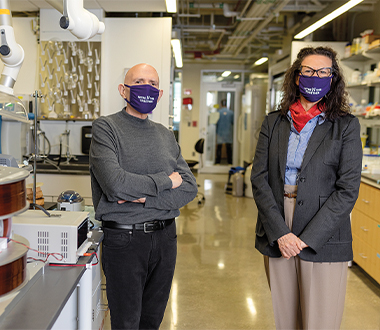
Samuel Stupp, left, and Monica Olvera de la Cruz. Credit: Shane Collins
The Northwestern team used chemical synthesis to program the molecules within the hydrogel to respond to light. When exposed to light, the robot’s molecules become hydrophobic (repelling water), causing the water molecules to escape. This conversion causes the robot to “come alive” by bending from a flat position to “standing.” The researchers discovered that this bending enables the material to respond rapidly to rotating magnetic fields, activating its ability to walk fast.
“Eventually, we’d like to make armies of microrobots that could perform a complicated task in a coordinated way,” Stupp says. “We can tweak them molecularly to interact with one another to imitate the swarming of birds and bacteria in nature or schools of fish in the ocean. The molecular versatility of the platform could lead to applications that have not been conceived at this point.”
Reader Responses
No one has commented on this page yet.
Submit a Response